Dutch Made: discover the fantastic world of Hand-Engraver Kees Engelbarts (Video)
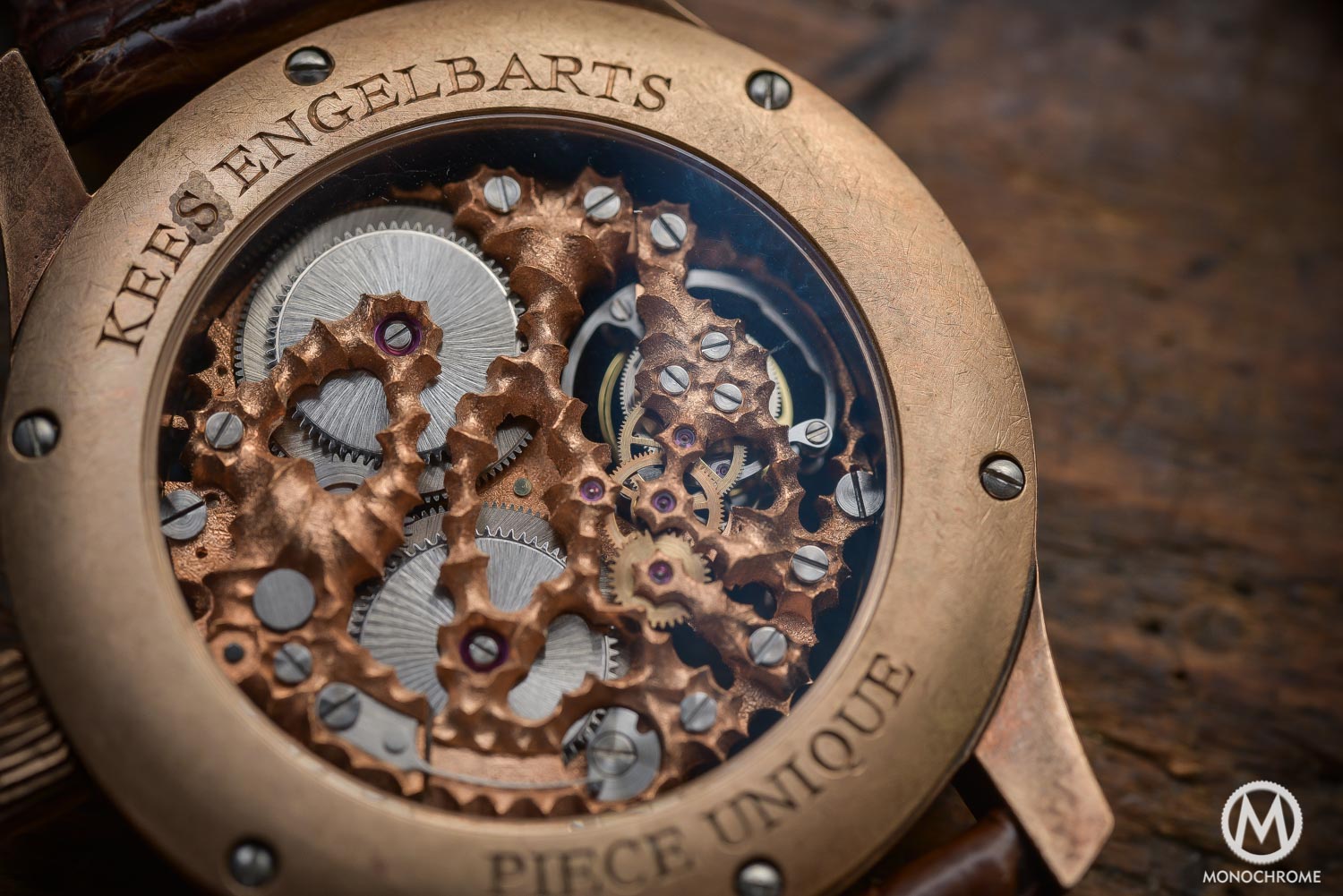
It’s not the first time that we show the work of master-engraver Kees Engelbarts. Kees is a Dutchman, moved to Geneva some 20 years ago to exercise his art (yes, his art…) in the land that is known for watchmaking. Besides commissioned work for high-end independent watchmakers and major brands alike, he also creates his own unique watches. Some of which we’ve covered here on Monochrome. Kees Engelbarts has always been on top of his game and he has created some of the most marvelous pieces that have ever been created. Lately Kees Engelbarts has been pushing the boundaries of skeletonizing. It’s hard to imagine how difficult it is to achieve such results, with a level a precision and devotion you can barely imagine. Kees is an artist in the fullest sense of the word, and today we let Kees explain his art in his own words. This is the first article of a series, dubbed Dutch Made, dedicated to Dutch folks in the watchmaking industry.
As a master-engraver Kees Engelbarts practices a complex, time-consuming and extremely precise craftsmanship. One major mistake and it’s back to square one and start all over again! Besides the engraving of dials and cases for third parties, he also creates watches under his own name and his watches are truly unique to the world of watchmaking. The level of skeletonizing Kees applies is rather extreme and he himself calls it “organic skeletonizing”. You could divide Kees’ work in two categories: watch that feature an engraved dial often with the use of Mokume-gane and timepieces that feature a seriously skeletonized movement.
Before you wil say, “that it is just another open-worked watch”, please read this (a quote from our editor in chief Frank Geelen from a previous article): “The moniker “skeleton watches” is often used for so-called open-worked watches, as well as for true skeleton watches. Before we go any further, let me briefly explain the difference. In short, open-worked watches feature an entire movement, or at least some movement parts, that are partially open. These movement parts are milled, usually by CNC machine, and might ultimately be finished by hand, might… A true skeleton watch starts its life with a normal non-open-worked movement that is skeletonized by the skillful hand of a master-engraver.”
Kees Engelbarts does the latter of course. it means that first, the master-engraver applies pressure, with a gouge, on the movement parts (think: mainplate, levers, gears, bridges) in order to create openings, and thus is done according to a plan. Of course the movement needs to keep its rigidity! The entire ‘framework’ of skeletonized bridges and mainplate must retain the necessary rigidity and strength to hold gears, barrels, gear-train and escapement in place. When a gear is just a tiny bit off balance, this will influence the functionality negatively. In order to retain good chronometric rates, and that’s something you certainly want especially with a tourbillon watch, gears must mesh perfectly, at plane level and everything has to work smoothly, without any friction. At a later stage Kees Engelbarts applies his artistic touch to make the “arms” of these bridges feel “organic”.
The second type of watches created by Kees feature (unusual) techniques from long-forgotten times. For instance, if you look at the watch below, you’ll see that it shows a texture that resemble vegetal mosses… How did Kees achieved this? Well, by experimenting, testing, trying new things, learning from faults and trying again. The main plate, visible from the front side of the watch, and that also serves as dial, has been achieved by literally bombarding the plate with a plasma cutter, to create holes and reliefs… Of course, this was not a smooth process and several attempts were required, but admit it, even if the final look is not to your taste, the texture achieved is simply unique and mesmerizing.
Finally, there is Mokume-gane, a ancient Japanese technique that Kees loves to use. It refers to a metalworking procedure which produces a mixed-metal laminate with distinctive layered patterns. Mokume-gane translates best to “wood grain metal”. Traditional components are relatively soft metallic elements and alloys which would form liquid phase diffusion bonds with one another without completely melting. Once a billet is achieved, pressure is applied on certain areas to create patterns – including this stunning and unique wood pattern (it is definitely made of metal and not wood). You can observe the thinness of the engravings done on the birds and leafs, and do consider that for the naked eye these dial elements seem to have a lot of depth. In reality the dial and every element on it, is less than 5mm thick. Go figure…
This why Kees Engelbarts, without being egocentric, can modestly say “I sign my watches on the backside, similar to a painter or a sculptor who puts is name on a finished piece“. As French people would say, bravo l’artiste!
You can contact Kees Engelbarts through his website (kees.ch) or Facebook page.
2 responses
Thanks Very interesting, I’d never heard of this guy before.
Although I am not a fan of the styling, I am so impressed with his “Skillset”. Hand engraving in the US is very hard to find, in major cities you may find a few! I can’t begin to estimate the hours dedicated to this work … Truly an art form which he has mastered! Thanks for the view..Mike Cotter